Antibacterial fiber processing method
Antibacterial fiber processing method
Fibers or textiles can play two roles after antibacterial and deodorant treatment: one is to protect people who use textiles, if antibacterial textiles can kill bacteria such as Staphylococcus aureus, white fungus, Escherichia coli, Trichophyton rubrum and Fungi can prevent the spread of infectious diseases; prevent malodors in underwear and socks; prevent the growth of athlete's foot on the socks; prevent erythema from diapers; improve the immunity of the elderly and patients; and prevent cross-infection in hospitals. The second is to prevent fiber damage. Because it has various molds such as Aspergillus niger and Penicillium, it can prevent discoloration, brittleness of the fiber material and mildew of the textile during storage.
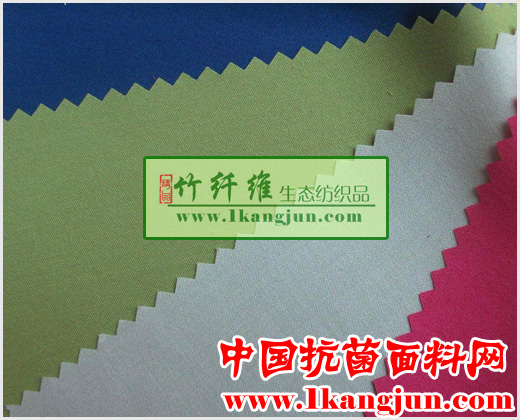
At present, there are two types of antibacterial fibers that are relatively mature and have been industrially produced: one is an inorganic antibacterial antibacterial fiber represented by a synthetic fiber containing nano-scale silver zeolite antibacterial material, and the fiber is safe and durable to human body. . The second is an antibacterial fiber developed by blending and spinning a high temperature resistant organic antibacterial agent. These antibacterial fibers use an organic antibacterial agent that is safe to the human body and has a broad spectrum of antibacterial effects against Gram-positive bacteria, Gram-negative bacteria, molds and sputum bacteria, with high antibacterial rate and good durability.
The main methods for manufacturing antibacterial fibers are as follows:
1. Blending spinning method
There are many methods for manufacturing antibacterial fibers. For example, chemical grafting or modification of the polymer structure of chemical fibers can also be carried out by physically mixing the antibacterial agent into the fiber, or by using a composite spinning technique, etc., in which the blending method is applied. More, that is, in the spinning stage of the synthetic fiber, the antibacterial agent is mixed into the polymer for spinning. The operation of mixing the antibacterial agent into the fiber may be carried out in the polymerization stage of the high polymer, after the end of the polymerization, before the melt spinning of the polymer, and the fiber may be mixed in the spinning dope even when the fiber such as rayon or acrylic fiber is wet-spun. The antibacterial agent mixed in the melt spinning is required to have high heat resistance and safety. The biggest advantage of the method is that the process is simple, the cost is low, and the use is safe because of the small amount of dissolution, but the use of high-efficiency antibacterial agent is required. The disadvantage is that the effect of the antibacterial agent is small when the amount of the antibacterial agent is small; the antibacterial agent has a large amount of influence on the spinning performance of the fiber.
The blend spinning method is to mix an auxiliary agent such as an antibacterial agent and a dispersing agent with a fiber matrix resin, and to produce an antibacterial fiber by melt spinning. According to this method, the antibacterial agent is subjected to a process of melt mixing, spinning, stretching and the like with the matrix resin, and the antibacterial agent is required to have good temperature resistance and the particle diameter is sufficiently small.
In the spinning process, the antibacterial agent is blended into the polymer and mixed and spun. For wet spinning, a suitable finishing agent is dissolved in an organic solvent and added to the spinning raw material. In the melt spinning, the finishing agent is made into an antibacterial masterbatch, and then melted and spun after being blended with the raw material. Such an antibacterial agent is required to have high temperature resistance and has good dispersibility and compatibility with the polymer.
The early antibacterial agents for chemical fiber blending are generally metal ion-containing composites, many of which contain heavy metal ions. In recent years, with the increase of environmental awareness, the ecological toxicity of heavy metal ions to human body Has gradually been taken seriously, antibacterial agents with high antibacterial effect but high toxicity have been gradually phased out, replaced by metal ion-containing compounds, currently used is harmless metal oxides, salts or Active metal ions on the support and the metal compound, such as Ag-containing zeolite, Zn, Cu composite or TiO 2 . The antibacterial agent has a broad-spectrum antibacterial effect, is harmless to the human body, and has good thermal stability, and is advantageous for blending and spinning. It is reported that the antibacterial fiber prepared by this method has an antibacterial rate of only 70% to 80%, and the antibacterial effect is not ideal. Since 1995, Jlsun(R) permanent antibacterial fiber has been successfully developed. It is harmless to the human body, has good compatibility with fiber materials and has a broad-spectrum antibacterial effect. It can still be washed after dozens of standard methods. Maintaining an antibacterial rate of more than 90% and having the same fiber properties as conventional fibers, the research and production of permanent antibacterial fibers has reached a new level.
The blended spinning modification method is used to obtain permanent antibacterial fibers that fully meet the safety requirements, which provides a very broad space for the development of various antibacterial textiles. For some hospital-specific sanitary materials and various sanitary products, it is not only easy to use, but also does not have to go through various complicated disinfection procedures. Even if it is stored for a period of time, it will not be contaminated by bacteria. On the top, the overall cost is lower. The emergence of safe antibacterial fiber with permanent antibacterial effect and the production process has opened up a new world for the development of antibacterial textiles. With the enhancement of people's health and environmental awareness and the improvement of the quality of life, people not only have a greater demand for textiles with antibacterial and deodorant properties, but also put forward higher requirements for safety and durability, while permanent antibacterial fibers are being It meets the requirements of high efficiency, broad spectrum, safety, durability and wide applicability. It is expected that this high-tech new antibacterial fiber product will surely achieve greater development.
At present, the common blended antibacterial fibers are as follows:
(1) Antibacterial fine denier polypropylene filament
The processing technology is divided into antibacterial masterbatch configuration, spinning and drafting and three-step method for production:
Antibacterial masterbatch manufacturing: Due to the addition of antibacterial powder, the difficulty of spinning polypropylene fine denier is increased. Therefore, the manufacture of masterbatch is an important process link, which solves the coupling and uniform dispersion of powder and polypropylene carrier. technology. For example, the special zeolite SiO2/Al2O3 is used as a carrier, and reacts with heavy metal ions such as antibacterial Ag+, Cu2+, Zn2+, so that the metal ions are uniformly adsorbed into the powder, and the appropriate coupling agent and dispersing agent are added together into the high-speed mixer. Under certain temperature conditions, high-speed mixing can be made into antibacterial powder for polypropylene for a certain period of time, and then the powder is mixed with a certain proportion of polypropylene material, and extruded, formed, and pelletized by a twin-screw extruder. Antibacterial masterbatch. In the application of nano-powder fibers, masterbatch technology is particularly important to solve this problem, so that the application of nano-powder in the field of fine-denier filament spinning can be realized.
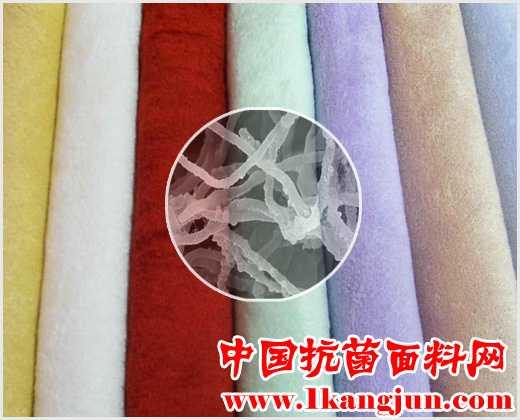
In addition, if the antibacterial polypropylene chips have the spinnability of high-speed spinning, it is necessary to consider the molecular weight and its distribution, the melt index, the masterbatch carrier and other technical indexes, and adjust to a suitable processing technology.
(2) Inorganic antibacterial polyester fiber
The inorganic antibacterial polyester fiber is another antibacterial fiber produced by a blending method. The method for producing polyester antibacterial fiber is firstly made into a nano-layered silver-based antibacterial agent or an antibacterial masterbatch having a high content of AgION containing silver inorganic zeolite, and a certain proportion of antibacterial masterbatch is added during spinning, and the method of blending and spinning is adopted. Made of polyester antibacterial fiber or antibacterial hollow fiber. The production process includes a slicing drying process, a spinning drafting process and the like. The production of such fibers are the United States KOSA Company, Beijing Jieer Shuang Company, Jiangsu Yihua Company, Japan Kuraray Company, Germany Trevira Company.
(3) JLSUN (R) antibacterial fiber
In 1997, the high-temperature antibacterial finishing technology invented over the years was successfully applied to synthetic fibers, and a series of antibacterial fibers and masterbatch such as antibacterial polypropylene filament and antibacterial polyester staple fiber were developed. Among them, fine denier and ultrafine denier antibacterial polypropylene filaments not only have excellent hydrophobicity, fast drying, stain resistance, moisture retention, light weight and soft handfeel, but also have broad-spectrum and long-lasting antibacterial properties.
Due to the production characteristics of fibers, general organic antibacterial agents are not well used in the production of antibacterial fibers, but some organic antibacterial agents have good high temperature stability and can be used to produce antibacterial fibers. For example, JLSUN (R) high temperature antibacterial agent SCJ, the main antibacterial component is a chlorobenzimidazole compound with a pyridoxamide structure. It acts on the cell membrane of bacteria, causing cell membrane defects, increased permeability, and leakage of cell contents; it can also hinder the synthesis of bacterial proteins, causing depletion of bacteria and protein bodies, leading to bacterial death. The antibacterial group carried by SCJ also selectively acts on the ergosterol of the fungal cell membrane, causing the cell membrane permeability to change, resulting in the loss of important substances in the bacteria and the death of the fungus.
The JLSUN(R) series of antibacterial products are produced using a blending technology route. Firstly, the SCJ high temperature resistant antibacterial agent produced by Beijing Jieer Shuang Company was blended with the slice carrier to prepare antibacterial masterbatch, and various antibacterial fibers were prepared by blending and spinning a certain proportion of antibacterial masterbatch and high polymer. These products have long-lasting antibacterial effect. After testing, JLSUN(R) antibacterial fiber products have the characteristics of broad-spectrum antibacterial, long-lasting antibacterial effect, non-toxic and non-irritating to the skin, and safe for human body. The whiteness and mechanical and physical properties of JLSUN(R) antibacterial fiber are no different from the corresponding conventional fibers, and have wide applicability. The JLSUN(R) antibacterial fiber series products that have been developed and produced include: polyester (filament, staple fiber), polypropylene (filament, staple fiber), nylon (filament, and stretched wire). Products can be widely used in underwear, socks, sterile surgical gowns, surgical caps, antibacterial clothing, shoe linings (pads), carpets, women's health care products, bedding, air conditioner filters and other filter materials.
JLSUN(R) antibacterial nylon-propylene composite fiber is made of nylon and polypropylene. During the high-temperature washing process of dyeing, the composite fiber becomes a single fiber with a single fiber fineness of 0.4d. This product can effectively kill Staphylococcus aureus, Neisseria gonorrhoeae (domestic strain), Streptococcus, pneumococcus, meningococcus, Escherichia coli, Shigella, Salmonella typhi, Klebsiella pneumoniae, Pseudomonas aeruginosa, Bacillus subtilis, wax Harmful bacteria such as Bacillus, Candida albicans, Fusarium oxysporum, Gypsum-like Trichophyton, Trichophyton rubrum, Penicillium, Aspergillus. Since the product is ultra-fine fiber and has a hydrophilic (nylon) and hydrophobic (polypropylene) structure, the fiber is woven into a textile, which has a distinct wicking effect, quick-drying, moisture-absorbing and breathable effects, and is very versatile. Soft, the fabric is shiny and elegant. This product is the material of choice for the production of high-end cool T-shirts and knitted underwear.
In commercial sales, JLSUN(R) antibacterial agent is called "antibacterial functional group", and "molecular assembly technology" is used to assemble an "antibacterial functional group" in a part of the resin (molecular chain) to make this part of the resin It becomes an antibacterial resin by itself.
Jlsun(R) antibacterial and deodorant polypropylene and polyester fiber have good safety, broad spectrum and high antibacterial property, excellent washing resistance, excellent processing property and excellent mechanical properties, and have good fiber appearance and hand feeling. The test and clinical application of many authoritative health units such as the Chinese Academy of Medical Sciences prove that antibacterial fabrics have obvious antibacterial, anti-inflammatory, deodorizing, anti-mildew, antipruritic and astringent effects, and can completely kill Staphylococcus aureus and epidermal grape that contact fabric. Cocci, Neisseria gonorrhoeae (domestic strain), Neisseria gonorrhoeae (international standard drug-resistant strain), Streptococcus, pneumococcus, meningococcus, Escherichia coli, Shigella, Salmonella typhimurium, Klebsiella pneumoniae, Pseudomonas aeruginosa, Bacillus subtilis, wax Bacillus licheniformis, Candida albicans, Fusarium oxysporum, Gypsum-like Trichophyton, etc., after 100 washings, the inhibition rate is still above 99.95%, against Aspergillus niger, Aspergillus flavus, P. citrinum, Trichoderma viride , ball sclerotium, etc. have 0 to 1 level of antibacterial effect (GB/T2423.16-1999). No irritation to the skin, no allergic reaction, no toxicity to the human body, can effectively prevent infection of trachoma, conjunctivitis, gonorrhea, vaginitis, cervicitis, pelvic inflammatory disease, prostatitis, respiratory infections, etc.癣, eczema, sweat odor, foot odor, skin itching, etc. have significant effects.
(4) Anti-mite, antibacterial multifunctional fiber
Dust mites feed on human dander, with a body size of about 300 microns and a feces of between 10 and 40 microns. These dust mites and excretions contain allergens that cause asthma, dermatitis or rhinitis. The SCJ-998 high-efficiency anti-mite antibacterial agent is added to the acrylic spinning dope to obtain anti-mite and antibacterial fibers. Its anti-mite and anti-bacterial properties have been tested by relevant national authorities and have excellent anti-mite and anti-bacterial properties. The dust mite repellent rate is 99%, the antibacterial rate is 99.9%, and it is not allergic to skin and non-irritating. The use of anti-mite antibacterial acrylic fiber is suitable for all types of textiles and blended fabrics, including clothing, bedding, mattress lining, pillow core, core, carpet, toy, air filter and other products.
Similar products abroad include Amicor antibacterial fiber from Acordis, UK. It has a built-in design, like an antibacterial warehouse inside the fiber. Through the principle of concentration gradient, the antibacterial agent is continuously dissolved on the fiber surface. The finished textile can be subjected to repeated washing without reducing its antibacterial properties. Antibacterial agent is an antibacterial agent widely used in toothpaste and sputum. It is harmless to the human body and is an agent that inhibits the reproduction of harmful bacteria and has high safety to human body. Three series of antibacterial yarns have been developed: antibacterial, antifungal and anti-aphid.
The Irish company Wrllmqn also launched the Fillwell Wellcare series of durable filler fibers on the market. This fiber has a role in controlling the reproduction of bacteria and dust mites on soft decorations, mainly by adding additives to the fibers during the production process, so the decorations produced by them have antibacterial and anti-caries effects throughout their lifetime. Mainly used for bedding. Since the antibacterial and anti-caries agent is permanently fixed to the fiber, it will take effect when it comes into contact with microorganisms. The bacteria decreased by 99% within 24 hours, and the total number of dust mites decreased by 99% during the four weeks, and the full effect was maintained after 50 washes. Other properties are not affected by additives such as warmth and comfort.
(5) Antibacterial acrylic and nylon
In the processing method, for example, in the synthetic fiber production stage, a metal such as silver is fixed to the zeolite skeleton by an ionic bond, and the antibacterial agent is added to a polymer such as polyacrylonitrile or polyamide to knead the spinning to slightly disperse the antibacterial agent. Inside the fiber and on the surface, the fiber itself contains an antibacterial agent. This method exhibits an antibacterial action by an antibacterial agent on the surface of the fiber and a partially dissolved antibacterial agent. [33] Representative products such as "Biosafe" of Japan's Zhongfang Synthetic Fiber Company, "Nonsemll" of Fusuke, "Commuting Fast" by Reynolds and "Taizikon" of Teijin.
2, composite spinning method
Antibacterial products can also be developed using composite spinning technology. The composite spinning method is an antibacterial fiber having a structure of a side-by-side type, a core-sheath type, a mosaic type, a hollow multi-heart type, etc., by using a fiber containing an antibacterial component and a fiber or a fiber which does not contain an antibacterial component. Incorporating the antibacterial fiber into the skin layer of the fiber or making it a side-by-side component of the side-by-side type composite fiber, especially for the former, the antibacterial agent can be added only to the skin layer, which not only saves raw materials, but also facilitates Maintain the basic properties of the fiber. This method is the development direction of antibacterial synthetic fibers. The antibacterial fiber produced by the method has the same requirements as the blend spinning method because it also undergoes a process of melting and spinning.
One of the representatives of this product is the “Liparthai†two-component antibacterial deodorizing PET fiber developed by Teijin Corporation of Japan. The fiber is a side-by-side structure, mainly composed of an antibacterial agent and a deodorant. It has excellent antibacterial and deodorizing effects.
Another well-known antibacterial fiber with a sheath-core structure is Foss fiber from Foss, USA. The bicomponent fibers in Foss fiber are specially designed so that AgION is only in the skin and is optimized for harmful bacterial contact surfaces. Experiments have shown that AgION can eliminate 99.99% of infectious and odor-causing bacteria. The fiber is very stable even in extremely severe production conditions. It can withstand high temperatures of 800 ° C and has a stability at pH 3-10. Foss fiber containing AgION can also be blended with other additives or blended with other fibers to form flame retardant, UV resistant, conductive, stain resistant and moisture permeable properties.
3. Chemical graft modification method
A processing method for imparting antibacterial properties to fibers by modifying the surface of the fibers and then bonding the antibacterial groups by coordination chemical bonds or other types of chemical bonds. That is to use chemical modification technology.
The chemical modification of the grafting method to prepare the antibacterial fiber requires that the surface of the fiber be combined with the antibacterial group. The gene of the antibacterial finishing agent is grafted onto the reaction group on the surface of the fiber, and for the substance not having the reactive group, the reactive group is introduced to make the fiber have chemical modification conditions. A typical representative is a copper sulphide composite. The copper removal is controlled during the manufacture of the copper ammonia fiber, and the copper compound is dispersed in the fiber and vulcanized. There is also the "Sandallon SS-N" of Japan's residual hair dyeing company, which uses copper-containing substances as an antibacterial finishing agent, and uses a dyeing method to combine the copper ions with the amino groups on the nylon fibers on the surface of the fibers. A strong copper sulfide coating layer is formed thereon, so that the fiber has excellent electrical conductivity, durable antibacterial property and safety of use.
The preparation of antibacterial fibers by chemical grafting is generally carried out in two steps: in the first step, the fibers are surface treated and treated to produce a point of action on the surface of the fibers which can be grafted with the antibacterial group compound. The current common methods for fiber surface treatment are chemical solvent treatment and radiation. In the second step, a compound having an antibacterial group is combined with the treated fiber to obtain an antibacterial fiber.
4, natural antibacterial chemical fiber
(1) Chitin fiber and chitosan fiber
Chitin or chitosan can be dissolved in a suitable solvent. If a solution of a certain concentration and a certain viscosity has a good spinning strength, it can be made into a filament or a short fiber by wet or dry spinning. . Chitin or chitosan fibers are viscose fibers. Chitin fiber textiles have strong antibacterial activity, and the test shows that it has strong inhibition against Gram-positive bacteria (Staphylococcus aureus) and Gram-negative bacteria (Escherichia coli), mold (Candida albicans), etc. The ability and bacteriostatic ability reached 100%, 70.43% and 50.11%, respectively.
On the basis of maintaining the excellent functionality of chitosan fiber, in order to further improve the quality index of chitosan fiber and reduce the production cost, countries have developed a blending process of chitin, chitosan fiber and other fibers. Among them, the physical blending spinning method is one of the most common methods. The chitosan and chitin are pulverized to a certain extent and uniformly dispersed in a spinning slurry such as viscose, acrylic, vinylon, etc., and the fiber contains a certain amount of chitin and chitosan through the spinning process, so the product has a shell polycondensation. Good antibacterial properties of sugar.
Chitosan and chitin viscose antibacterial fibers are currently produced on a large scale. In the international market, new products of viscose fiber have entered the ranks of high-end apparel fabrics, and the addition of chitosan and chitin can also make fibers have the advantages of low irritation, high moisture retention, softness and bacteriostasis.
Fujito's Chitogreen is a natural fiber antibacterial ingredient, chitin, which is added to the fiber and has a unique method to improve the precision. Chitogreen can destroy the cell membrane of bacteria, but it does not enter the skin cells of the human body. Irritating, even people with sensitive skin can use it with confidence. Due to the fixed composition, it has an overwhelming wash durability. It is suitable for use in hospital uniforms, bed sheets, bath towels and other items that require repeated washing. In addition to its long-lasting antibacterial properties, it also has superior hygroscopicity and soft touch. Fujitsu has expanded its use in interior and exterior garments and curtains.
(2) Bamboo fiber
Chinese medicine believes that bamboo leaves, ru, leaching, spring, bamboo shoots, fine, and frost can all treat diseases. Bamboo leaves have the functions of clearing heat, removing annoyance and diuresis; Zhuru has the effects of clearing heat, removing phlegm, removing irritability and vomiting; bamboo spring can diarrhea, phlegm, and cool heart; bamboo leaching is used for heat and phlegm . Bamboo itself has antibacterial properties, so that it has no insects and no decay during the growth process. According to the data, in the production process of bamboo fiber, the high-tech process is used to prevent the antibacterial substance from being destroyed, so that it is always bound to the cellulose macromolecule. Bamboo fiber fabrics will not lose their antibacterial effect after repeated washing and sun exposure. After testing, the bamboo fiber product has an antibacterial rate of 71% for 24 hours, which proves that harmful microorganisms such as bacteria can not only survive for a long time in bamboo fiber products, but also reduce or even disappear in a short time. However, in the author's experiment, it was found that the inhibition rate of bamboo fiber was less than 60%. The author believes that this is because the production process of bamboo fiber is similar to that of viscose fiber. The original antibacterial substance is destroyed in the process of strong alkali or sulfonation, so that the antibacterial property of bamboo fiber is much lower than that of natural bamboo.
5, pure natural fiber
Hemp fiber is a natural antibacterial fiber. Hemp fiber has unique anti-mildew and bactericidal effect. The result of qualitative bacteriostatic test of hemp textile without any drug treatment and washing shows that it has different Staphylococcus aureus, Pseudomonas aeruginosa and Candida albicans. The degree of bacteriostatic effect. Folk cannabis rope sausages, naps, sealed cans, etc. are strong and not rot. Based on this anti-mildew, deodorant and anti-corrosion function, hemp textiles can also be used for food packaging, sanitary materials, footwear, ropes, and the like. Today, the world is advocating the concept of green and environmental protection. Cannabis, which has a long history, once again enters the human eye. Hemp fiber has been widely used in the garment processing industry due to its unique characteristics of natural inhibition, coolness, softness, anti-static and heat resistance.
In addition, ramie, flax, and apocynum, they also have natural antibacterial and antibacterial functions.
[China Antibacterial Fabric Network ]
ZeroClipboard.setMoviePath('/plugin/copytofriends/ZeroClipboard.swf'); var clip = new ZeroClipboard.Client(); clip.setHandCursor(true); clip.setText(" Processing method of antibacterial fiber http:// .com/post307/"); clip.addEventListener('complete', function(client,text){ alert("Successfully copy this article to the clipboard!"); }); clip.glue('copytofriends');
Winter Warm Top,Heavy Knit Top,Lace Stitching Knit Top,Geometric Joining Knit Top
SHAOXING CHENYEE TEXTILE CO. LTD , https://www.fabriccy.com